Institute of Physics of Materials AS CR, v. v. i. > Groups > High Cycle Fatigue Group
The research activities in the high cycle fatigue group are focused on the study of the nature and quantitative description of the fatigue processes in all fatigue stages. The main goal of the research is to contribute to better understanding of cyclic plasticity at low amplitudes, crack initiation and threshold values of fatigue crack propagation and to the fracture-mechanical description of the fatigue crack behaviour. Theoretical and experimental studies are focused on the relation between microstructure, microstructure evolution during damage progress, and macroscopic fatigue and fatigue/creep properties. The numerical estimation of the fracture parameters and simulations of the fracture behaviour are an important part of the research as well. The formulation of crack stability criteria for non-homogenous materials, notches and layered structures is a live issue studied in the group. Owing to this, the spectrum of studied materials is rapidly increasing. At present non-metallic materials such as polymers, polymer or ceramic based composites and advanced building materials are also dealt with.
In close cooperation with some industrial companies, the lifetime of advanced components is predicted based on numerical simulations and advanced fatigue tests.
The research of fatigue phenomena started at the IPM under the leadership of Prof. Mirko Klesnil in the 1960s. From the mid 1980s to 2010 the head of the high cycle fatigue group was assoc. Prof. Petr Lukáš, a well-known expert in the field of basic mechanisms of fatigue. The theoretically and computationally oriented part of the research group was established in the 1980s by Prof. Zdeněk Knésl, who was a natural and respected supervisor. The present staff of the group can be found here.
The main research projects currently running:
Electrodynamic fatigue testing system Instron E20000
Contact person: Ing. Michal Jambor, Ph.D.
The Instron E20000 is a universal testing system for dynamic and static testing of material properties, with a capacity of 20 kN in dynamic mode and 14 kN in static mode.
INSTRON E10000 with linear motor technology, push-pull, torsion
Contact person: prof. Ing. Pavel Hutař, Ph.D.
An electrodynamic testing instrument INSTRON with closed control loop for static or dynamic testing from very small to high frequencies (100 Hz and more).
INSTRON E3000 with linear motor technology
Contact person: prof. Ing. Pavel Hutař, Ph.D.
Electrodynamic testing instrument INSTRON with closed control loop for static or dynamic testing from very small to high frequencies (200 Hz and more). Maximal load is of ±3000 N for dynamic testing and ±2100 N for static testing. The system is equipped with temperature controlled chamber INSTRON 3119-605 with a temperature range from -100°C in LN2 atmosphere (-70 °C in CO2) to 350 °C and the internal dimensions of 485×240×230 mm.
Resonant system Amsler 10 HFP 1478, 100 kN, push-pull
Contact person: prof. Ing. Pavel Hutař, Ph.D.
Resonant pulsator dedicated mainly for fatigue tests at high temperatures. The testing device is equipped by furnace with possible heating up to 1000 °C. Work resonant frequency is controlled by electromagnetic actuator. Test frequency is adjustable and is usually in range of 100 to 130 Hz. Movable crosshead of the pulsator enables application of mean force loads, i.e. asymmetrical fatigue tests.
Resonant system Amsler 20 HFP 5100, push-pull
Contact person: prof. Ing. Pavel Hutař, Ph.D.
A resonant electromagnetic pulsator is equipped by accessories for testing compact tensile specimens and 3 point bending test dedicated mainly for fatigue crack propagation measurements. Therefore, the pulsator is upgraded by pair of a camera system for fine measurement of actual crack length. The maximal load is ±10 kN for dynamic testing and ±20 kN for static testing. Test frequency can be in the range of 30 to 300 Hz.
Resonant system Schenck PVQ, 60 kN, push-pull
Contact person: prof. Ing. Pavel Hutař, Ph.D.
Resonant pulsator with mechanical actuator. Possible test frequencies are from 12 to 83 Hz. Test machine is suitable for force controlled fatigue tests of larger samples thanks to the size and stiffness of frame. Dynamic load can be up to 30 kN and mean load up to 36 kN. The pulsator is dedicated for fatigue crack propagation tests of flat specimens (push/pull or push/push tests) or 3 point bending test specimens.
Resonant system ZwickRoell Vibrophore 25, push-pull, temperature up to 1200 °C
Contact person: prof. Ing. Pavel Hutař, Ph.D.
A resonant electromagnetic pulsator is designed for dynamic testing of materials. Determination of fatigue life (S-N curve) or fatigue crack propagation (CT specimens) can be measured at room or high temperatures (up to 1200 °C).
Servohydraulic system Zwick/Roell Amsler HC25, push-pull
Contact person: Ing. Petr Miarka, Ph.D.
Compact table model of servo-hydraulic pulsator dedicated for static and dynamic material testing. Pulsator is capable to load the specimen by forces up to 25 kN. Maximum stroke of grips is 250 mm. Testing device is able to control mechanical tests in control regime of force or displacement. Electronic controlling system enables tailoring of a course of the mechanical test according to operator needs. Zwick/Roell Amsler HC25 is mainly determined for fatigue tests with low frequencies and with needs of fine level of control.
Ultrasonic system for very high cycle fatigue measurements
Contact person: doc. Ing. Jan Klusák, Ph.D.
Ultrasonic fatigue system pulsating at frequency of 20 kHz. This allows real-time measurement of very high cycle fatigue properties of materials at the number of cycles between 10 million to 10 billion. Measurement is possible under tension/compression and tension/tension conditions. It enables the measurement of SN (Wöhler) curves and fatigue crack propagation rates.
all publications
High Cycle Fatigue Group
Head | Ing. Michal Jambor, Ph.D. |
[javascript protected email address] | |
Phone number | +420 532 290 414 |
Room | 119 |
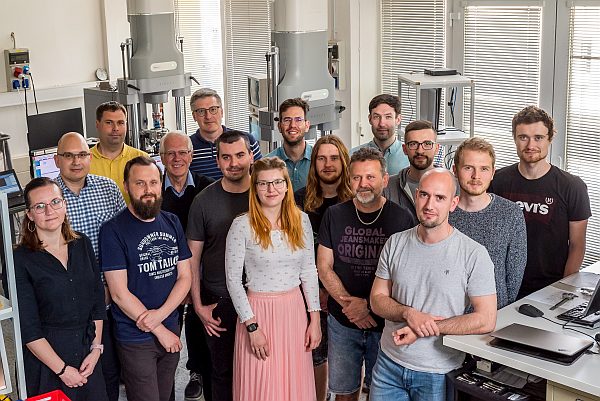
In close cooperation with some industrial companies, the lifetime of advanced components is predicted based on numerical simulations and advanced fatigue tests.
The research of fatigue phenomena started at the IPM under the leadership of Prof. Mirko Klesnil in the 1960s. From the mid 1980s to 2010 the head of the high cycle fatigue group was assoc. Prof. Petr Lukáš, a well-known expert in the field of basic mechanisms of fatigue. The theoretically and computationally oriented part of the research group was established in the 1980s by Prof. Zdeněk Knésl, who was a natural and respected supervisor. The present staff of the group can be found here.
The main research projects currently running:
- fatigue and fatigue/creep behaviour of single crystalline and polycrystalline superalloys,
- fatigue properties of ultrafine-grained materials,
- effect of mean stress on the cyclic stress-strain response and fatigue life,
- effect of notches (including bi-material notches) and cracks on fatigue life and fatigue/creep life,
- effect of a free surface on fatigue crack behaviour,
- physical consequences of the constraint,
- effect of the interface between two materials on a crack or notch behaviour,
- basic fatigue and fracture characteristics of advanced building materials,
- description of the crack behaviour in polymer materials,
- description of the crack behaviour in advanced composite materials.
Researchers
Name | Phone numbers | Rooms | |
---|---|---|---|
Ing. Pavol Dlhý, Ph.D. | +420 532 290 338 | 108a | [javascript protected email address] |
doc. Ing. Stanislava Fintová, Ph.D. | +420 532 290 301 | 317 | [javascript protected email address] |
Ing. Roman Gratza, Ph.D. | +420 532 290 | [javascript protected email address] | |
prof. Ing. Pavel Hutař, Ph.D. | +420 532 290 351 | 223 | [javascript protected email address] |
prof. RNDr. Ludvík Kunz, CSc., dr. h. c. | +420 532 290 379 | 112 | [javascript protected email address] |
prof. Ing. Luboš Náhlík, Ph.D. | +420 532 290 358 | 416 | [javascript protected email address] |
Ing. Jan Poduška, Ph.D. | +420 532 290 338 | 108a | [javascript protected email address] |
Ing. Pavel Pokorný, Ph.D. | +420 532 290 362 | 108 | [javascript protected email address] |
Ing. Karel Slámečka, Ph.D. | +420 532 290 338 | 108a | [javascript protected email address] |
Ing. Miroslav Šmíd, Ph.D. | +420 532 290 421 | 106 | [javascript protected email address] |
Ing. Tomáš Vojtek, Ph.D. | +420 532 290 362 | 108 | [javascript protected email address] |
Postdocs
Name | Phone numbers | Rooms | |
---|---|---|---|
Ing. Lukáš Trávníček, Ph.D. | +420 532 290 347 | 114 | [javascript protected email address] |
Phd students
Name | Phone numbers | Rooms | |
---|---|---|---|
MSc. Alfred Muchangi Murithi | +420 532 290 347 | 114 | [javascript protected email address] |
Ing. Radek Kubíček | +420 532 290 347 | 114 | [javascript protected email address] |
Ing. Dušan Tichoň | +420 532 290 347 | 114 | [javascript protected email address] |
Technicians
Name | Phone numbers | Rooms | |
---|---|---|---|
Michal Minařík | +420 532 290 361 | 107 | [javascript protected email address] |
Diploma students
Name | Phone numbers | Rooms | |
---|---|---|---|
Bc. Vojtěch Bartošík | +420 532 290 421 | 106 | [javascript protected email address] |
Bc. Václav Dziubek | +420 532 290 347 | 114 | [javascript protected email address] |
Kateřina Neumannová | +420 532 290 421 | 106 | [javascript protected email address] |
Dalibor Pavelčík | +420 532 290 336 | 128b | [javascript protected email address] |
Project number | Name | Investigator |
---|---|---|
CZ.02.01.01/00/23_020/0008549 | Partnership for Security in Sustainable Transport and Energy | prof. Ing. Luboš Náhlík, Ph.D. |
CZ.02.01.01/00/22_008/0004634 | MEBioSys - Mechanical engineering of biological and bio-inspired systems | prof. Ing. Pavel Hutař, Ph.D. |
23-07235S | Microstructural manipulation of austenitic steels by laser powder bed fusion technique | Ing. Miroslav Šmíd, Ph.D. |
TN02000010 | National Competence Centre of Mechatronics and Smart Technologies for Mechanical Engineering | prof. Ing. Pavel Hutař, Ph.D. |
TN02000018 | National Centre of Competence ENGINEERING | prof. Ing. Luboš Náhlík, Ph.D. |
CK03000060 | Advanced design methodology of railway axles for safe and efficient operation | prof. Ing. Luboš Náhlík, Ph.D. |
Project number | Name | Investigator |
---|---|---|
22-28283S | Oxide-induced crack closure and its implications for lifetime prediction of mechanical components (OXILAP) | prof. Ing. Pavel Hutař, Ph.D. |
FW03010149 | New wheel design for freight transport with higher utility properties | prof. Ing. Pavel Hutař, Ph.D. |
FW03010190 | Advanced precision casting technologies for new types of blade castings and blade segments of gas turbines and turbochargers from modern superalloys with increased service life | prof. Ing. Pavel Hutař, Ph.D. |
FW03010504 | Development of in-situ techniques for characterization of materials and nanostructures | prof. Ing. Luboš Náhlík, Ph.D. |
CZ.01.1.02/0.0/0.0/20_321/0024465 | Research of resistance of casted radial wheels of turbochargers to thermomechanical stress and techniques of increasing mechanical values | prof. Ing. Pavel Hutař, Ph.D. |
CZ.01.1.02/0.0/0.0/19_262/0020138 | Research and development of casting technology of thermally affected parts of aircraft engines and highly precise casts of new generation of turbochargers | prof. Ing. Pavel Hutař, Ph.D. |
FW01010183 | Next Generation of Integrated Atomic Force and Scanning Electron Microscopy (GEFSEM) | prof. Ing. Luboš Náhlík, Ph.D. |
H2020-WIDESPREAD-2018-03 ID: 857124 | Structural Integrity and Reliability of Advanced Materials obtained through additive Manufacturing | prof. Ing. Luboš Náhlík, Ph.D. |
FV40327 | Automatic optical system for fatigue crack propagation measurement | prof. Ing. Pavel Hutař, Ph.D. |
LTI19 | The involvement of Czech research organizations in the Energy Research Alliance EERA | prof. Ing. Luboš Náhlík, Ph.D. |
TN01000071 | National Competence Centre of Mechatronics and Smart Technologies for Mechanical Engineering | prof. Ing. Pavel Hutař, Ph.D. |
TN01000015 | National Centre of Competence ENGINEERING | prof. Ing. Luboš Náhlík, Ph.D. |
19-25591Y | Effect of the microstructure on the fatigue in highly anisotropic stainless steel fabricated by selective laser melting | Ing. Miroslav Šmíd, Ph.D. |
FV40034 | Development of new design of railway axles with high operational reliability | prof. Ing. Luboš Náhlík, Ph.D. |
FV30219 | 3D print of implants for treating of a damaged skeleton, especially the human pelvis | prof. RNDr. Ludvík Kunz, CSc., dr. h. c. |
RFCS-02-2016 ID:747266 | Innovative approach to improve fatigue performance of automotive components aiming at CO2 emissions reduction (INNOFAT) | prof. Ing. Pavel Hutař, Ph.D. |
PCCL-K1 | K1-Center in Polymer Engineering and Science | prof. Ing. Pavel Hutař, Ph.D. |
CZ.01.1.02/0.0/0.0/15_019/0004399 | Research and development of precision casting technology for new type of aircraft engine castings and axial turbocharger wheels | prof. Ing. Pavel Hutař, Ph.D. |
RVO 68081723 | Long-term conceptual development of research organizations | prof. RNDr. Ludvík Kunz, CSc., dr. h. c. |
CZ.01.1.02/0.0/0.0/15_019/0004505 | Complex design of girders from advanced concretes | doc. Ing. Stanislav Seitl, Ph.D. |
17-01589S | Advanced computational and probabilistic modelling of steel structures taking account fatigue damage | doc. Ing. Stanislav Seitl, Ph.D. |
CZ.01.1.02/0.0/0.0/15_019/0002421 | Research and development of advanced precision casting technology of strongly thermally affected parts of new turbochargers from nickel based superalloys | prof. Ing. Pavel Hutař, Ph.D. |
GA15-09347S | Role reziduálních napětí v životnosti keramických kompozitů | prof. Ing. Luboš Náhlík, Ph.D. |
TA04011525 | Výzkum a vývoj technologií přesného lití radiálních kol turbodmychadel nové generace a nových typů lopatek plynových turbín. | prof. Ing. Pavel Hutař, Ph.D. |
CZ.1.07/2.3.00/45.0040 | Science Academy - critical thinking and practical application of scientific and technical knowledge in real life | doc. Ing. Jan Klusák, Ph.D. |
7AMB1-4AT012 | Development of new testing configurations for determination of relevant values of fracture characteristics of cementitious composites (DeTeCon) | doc. Ing. Stanislav Seitl, Ph.D. |
CZ.1.07/2.3.00/30.0063 | Talented postdocs for scientific excellence in physics of materials | prof. Ing. Luboš Náhlík, Ph.D. |
CZ.1.07/2.3.00/20.0214 | Human Resources Developments in the research of physical and material properties of emerging, newly developed and applied engineering materials | prof. Ing. Luboš Náhlík, Ph.D. |
CZ.1.07./2.3.00/20.0197 | Multidisciplinary team in materials design and its involvement into international cooperation | prof. Ing. Luboš Náhlík, Ph.D. |
M100411204 | Utilization of termographic techniques and advance probabilistic method for the efficient estimation of Wöhler curve parameters | doc. Ing. Stanislav Seitl, Ph.D. |
P108/12/1560 | Description of the slow crack growth in polymer materials under complex loading conditions | prof. Ing. Pavel Hutař, Ph.D. |
CZ.1.07/2.4.00/17.0006 | Building up Cooperation in R&D with the Research and Industrial Partners | prof. Ing. Luboš Náhlík, Ph.D. |
P105/11/0466 | Energetic and stress state aspects of quasi-brittle fracture – consequences for determination of fracture-mechanical parameters of silicate composites | doc. Ing. Stanislav Seitl, Ph.D. |
P104/11/0833 | Response of cement based composites to fatigue loading: advanced numerical modeling and testing | doc. Ing. Stanislav Seitl, Ph.D. |
GA ČR P108/10/2001 | Cyclic plastic deformation and fatigue properties of ultrafine-grained materials | prof. RNDr. Ludvík Kunz, CSc., dr. h. c. |
P108/10/2049 | Crack initiation and propagation from interface-related singular stress concentrators | doc. Ing. Jan Klusák, Ph.D. |
M100410901 | Fracture mechanics description of three dimensional structures: numerical analysis and physical consequences of constraint | doc. Ing. Stanislav Seitl, Ph.D. |
KJB200410901 | Fracture of silicate based composites studied on core drilled specimens – numerical-modeling background for advanced fracture parameters determination | doc. Ing. Stanislav Seitl, Ph.D. |
106/09/0279 | Fracture damage mechanism of multilayer polymer body | prof. Ing. Pavel Hutař, Ph.D. |
101/09/0867 | Assessment of fatigue damage of thin-walled structures | prof. Ing. Pavel Hutař, Ph.D. |
101/09/J027 | Correlation between structural changes, damage evolution and crack propagation behaviour of welded thermoplastics components | prof. Ing. Pavel Hutař, Ph.D. |
101/08/1623 | Innovative techniques for assessment of residual life of bodies with fatigue | doc. Ing. Stanislav Seitl, Ph.D. |
106/08/1409 | Role of Structure of Crosslinked Polymer Matrix in Particulate Composities. Multiscale Modeling and Experimental Verification. | prof. Ing. Luboš Náhlík, Ph.D. |
101/08/0994 | Determination of conditions of failure initiation in bi-material wedges composed of two orthotropic materials | doc. Ing. Jan Klusák, Ph.D. |
103/08/0963 | Basic fatigue characteristic and fracture of advanced building materials | doc. Ing. Stanislav Seitl, Ph.D. |
KJB200410803 | Generalization of linear elastic fracture mechanics to crack propagation problems in non-homogenous materials | prof. Ing. Luboš Náhlík, Ph.D. |
FT-TA4/023 | Research and development of mechanical properties of the materials used for new types of turbochargers ... | prof. RNDr. Ludvík Kunz, CSc., dr. h. c. |
AST5-CT-2006-030889 | Predictive Methods for Combined Cycle Fatigue in Gas Turbine Blades (PREMECCY) | doc. RNDr. Petr Lukáš, CSc., dr. h. c. |
106/06/P239 | The effect of free surface on fatigue crack growth | prof. Ing. Pavel Hutař, Ph.D. |
AV0Z20410507 | Physical properties of advanced materials in relation to their microstructure and processing | doc. RNDr. Petr Lukáš, CSc., dr. h. c. |
1QS200410502 | Properties of engineering materials under development applicable in the near future in traffic, medicine and power generating industry | prof. RNDr. Ludvík Kunz, CSc., dr. h. c. |
106/05/2112 | High-cycle fatigue of Ni-base superalloys at high mean stresses | prof. RNDr. Ludvík Kunz, CSc., dr. h. c. |
1P05ME804 | Fatigue behaviour of ultra fine-grained Copper and Magnesium alloy materials | prof. RNDr. Ludvík Kunz, CSc., dr. h. c. |
101/04/P001 | The influence of constraint on threshold values of the stress intensity factor | doc. Ing. Stanislav Seitl, Ph.D. |
106/04/P084 | Influence of the interface between two materials on fatigue crack propagation | prof. Ing. Luboš Náhlík, Ph.D. |
106/03/P054 | Linear Elastic Fracture Mechanics of Bi-material notches | doc. Ing. Jan Klusák, Ph.D. |
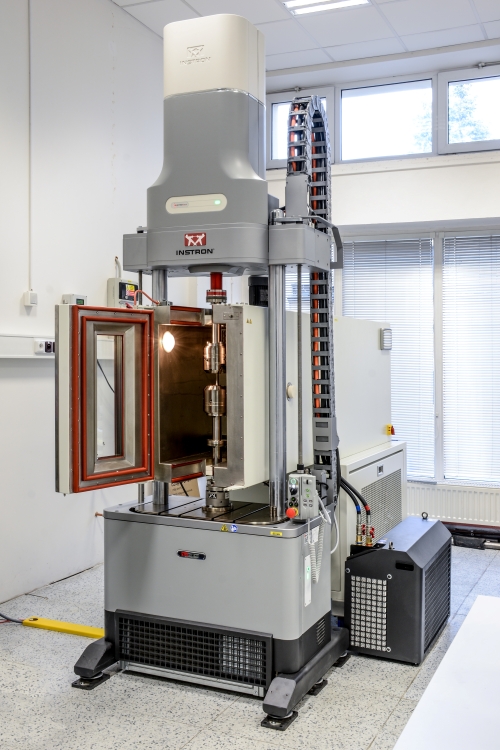
Contact person: Ing. Michal Jambor, Ph.D.
The Instron E20000 is a universal testing system for dynamic and static testing of material properties, with a capacity of 20 kN in dynamic mode and 14 kN in static mode.
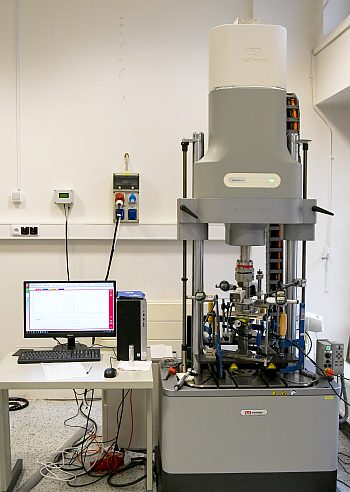
Contact person: prof. Ing. Pavel Hutař, Ph.D.
An electrodynamic testing instrument INSTRON with closed control loop for static or dynamic testing from very small to high frequencies (100 Hz and more).
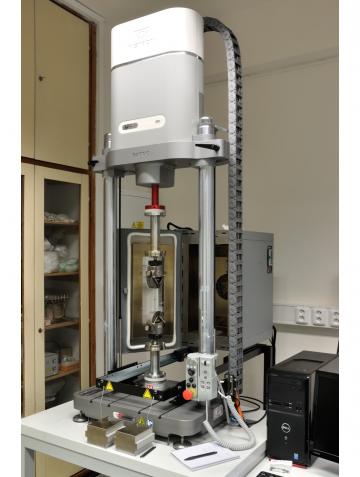
Contact person: prof. Ing. Pavel Hutař, Ph.D.
Electrodynamic testing instrument INSTRON with closed control loop for static or dynamic testing from very small to high frequencies (200 Hz and more). Maximal load is of ±3000 N for dynamic testing and ±2100 N for static testing. The system is equipped with temperature controlled chamber INSTRON 3119-605 with a temperature range from -100°C in LN2 atmosphere (-70 °C in CO2) to 350 °C and the internal dimensions of 485×240×230 mm.
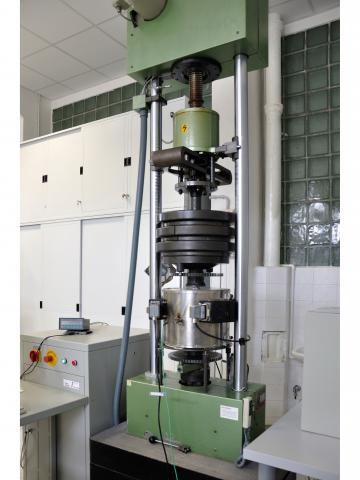
Contact person: prof. Ing. Pavel Hutař, Ph.D.
Resonant pulsator dedicated mainly for fatigue tests at high temperatures. The testing device is equipped by furnace with possible heating up to 1000 °C. Work resonant frequency is controlled by electromagnetic actuator. Test frequency is adjustable and is usually in range of 100 to 130 Hz. Movable crosshead of the pulsator enables application of mean force loads, i.e. asymmetrical fatigue tests.
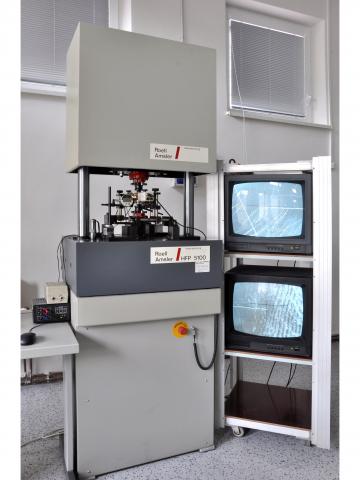
Contact person: prof. Ing. Pavel Hutař, Ph.D.
A resonant electromagnetic pulsator is equipped by accessories for testing compact tensile specimens and 3 point bending test dedicated mainly for fatigue crack propagation measurements. Therefore, the pulsator is upgraded by pair of a camera system for fine measurement of actual crack length. The maximal load is ±10 kN for dynamic testing and ±20 kN for static testing. Test frequency can be in the range of 30 to 300 Hz.
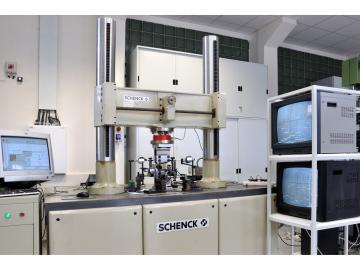
Contact person: prof. Ing. Pavel Hutař, Ph.D.
Resonant pulsator with mechanical actuator. Possible test frequencies are from 12 to 83 Hz. Test machine is suitable for force controlled fatigue tests of larger samples thanks to the size and stiffness of frame. Dynamic load can be up to 30 kN and mean load up to 36 kN. The pulsator is dedicated for fatigue crack propagation tests of flat specimens (push/pull or push/push tests) or 3 point bending test specimens.
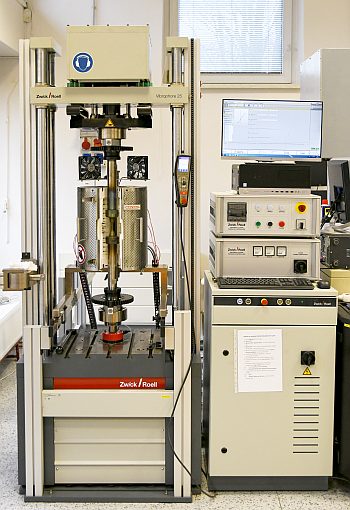
Contact person: prof. Ing. Pavel Hutař, Ph.D.
A resonant electromagnetic pulsator is designed for dynamic testing of materials. Determination of fatigue life (S-N curve) or fatigue crack propagation (CT specimens) can be measured at room or high temperatures (up to 1200 °C).
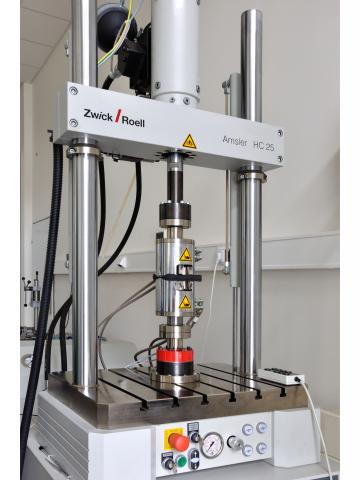
Contact person: Ing. Petr Miarka, Ph.D.
Compact table model of servo-hydraulic pulsator dedicated for static and dynamic material testing. Pulsator is capable to load the specimen by forces up to 25 kN. Maximum stroke of grips is 250 mm. Testing device is able to control mechanical tests in control regime of force or displacement. Electronic controlling system enables tailoring of a course of the mechanical test according to operator needs. Zwick/Roell Amsler HC25 is mainly determined for fatigue tests with low frequencies and with needs of fine level of control.
Carl Zeiss Jena Stereo Microscope
Contact person: Ing. Miroslav Šmíd, Ph.D.
Binocular stereoscopic microscope predetermined for observation of three-dimensional objects in reflected light.
Contact person: Ing. Miroslav Šmíd, Ph.D.
Binocular stereoscopic microscope predetermined for observation of three-dimensional objects in reflected light.
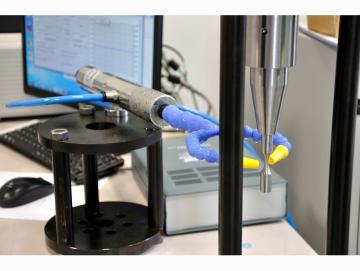
Contact person: doc. Ing. Jan Klusák, Ph.D.
Ultrasonic fatigue system pulsating at frequency of 20 kHz. This allows real-time measurement of very high cycle fatigue properties of materials at the number of cycles between 10 million to 10 billion. Measurement is possible under tension/compression and tension/tension conditions. It enables the measurement of SN (Wöhler) curves and fatigue crack propagation rates.
all publications