Institute of Physics of Materials AS CR, v. v. i. > Groups > Special Issues of Fracture Mechanics and Materials‘ Fatigue (FRACTIGUE)
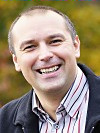
The research group focuses on determining the fracture mechanical and fatigue properties of materials beyond normal testing. In the case of fatigue loading of metals, it is beyond 107 cycles, in the case of concrete, for which fatigue tests are not normally performed, it is actually more than 1 cycle. Under these conditions, research into the relationship between the structure and properties of materials and failure mechanisms is very topical, especially for cases of new materials produced by additive technologies and for concrete building materials. Gigacycle fatigue materials research can serve as a source of material data for applications where a high number of cycles is critical, as well as for applications where high load frequency plays an important role. Within the group, we also focus on the assessment of stress concentrators related to shape changes or material changes (inclusions, interfaces in composites, etc.) in cases that have not yet been studied. In particular, we use and develop methods of generalized linear elastic fracture mechanics and methods of finite fracture mechanics, which always apply methods of assessing the stability of general stress concentrators in / at finite distances from the point of highest stress.
Servohydraulic pulsator Instron 8872, tension-compression with capacity of 25 kN
Contact person: Ing. Petr Miarka, Ph.D.
The servo-hydraulic pulsator is designed for static and dynamic testing of materials up to a force of 25 kN. The precision test control system allows control of the force and position (displacement) of the piston.
Servohydraulic system Zwick/Roell Amsler HC25, push-pull
Contact person: Ing. Petr Miarka, Ph.D.
Compact table model of servo-hydraulic pulsator dedicated for static and dynamic material testing. Pulsator is capable to load the specimen by forces up to 25 kN. Maximum stroke of grips is 250 mm. Testing device is able to control mechanical tests in control regime of force or displacement. Electronic controlling system enables tailoring of a course of the mechanical test according to operator needs. Zwick/Roell Amsler HC25 is mainly determined for fatigue tests with low frequencies and with needs of fine level of control.
Ultrasonic system for very high cycle fatigue measurements
Contact person: doc. Ing. Jan Klusák, Ph.D.
Ultrasonic fatigue system pulsating at frequency of 20 kHz. This allows real-time measurement of very high cycle fatigue properties of materials at the number of cycles between 10 million to 10 billion. Measurement is possible under tension/compression and tension/tension conditions. It enables the measurement of SN (Wöhler) curves and fatigue crack propagation rates.
all publications
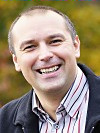
Special Issues of Fracture Mechanics and Materials‘ Fatigue (FRACTIGUE)
Head | doc. Ing. Stanislav Seitl, Ph.D. |
[javascript protected email address] | |
Phone number | +420 532 290 417 |
Room | 316 |
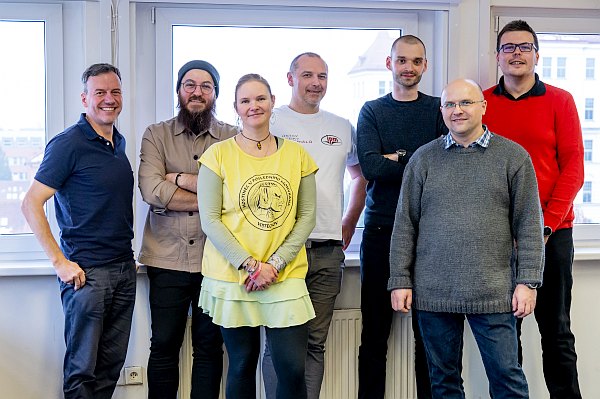
Researchers
Name | Phone numbers | Rooms | |
---|---|---|---|
doc. Ing. Jan Klusák, Ph.D. | +420 532 290 348 | 318 | [javascript protected email address] |
Ing. Lucie Malíková, Ph.D. | +420 532 290 367 | 604 | [javascript protected email address] |
Ing. Jan Mašek, Ph.D. | +420 532 290 430 | 603 | [javascript protected email address] |
Ing. Petr Miarka, Ph.D. | +420 532 290 430 | 603 | [javascript protected email address] |
Phd students
Name | Phone numbers | Rooms | |
---|---|---|---|
Ing. Mohammad Sami Al Khazali | +420 532 290 336 | 128b | [javascript protected email address] |
Ing. Pavel Doubek | +420 532 290 417 | 316 | |
Ing. Kamila Kozáková | +420 532 290 367 | 604 | [javascript protected email address] |
Ing. David Markusík | +420 532 290 430 | 603 | [javascript protected email address] |
Technicians
Name | Phone numbers | Rooms | |
---|---|---|---|
Pavel Cejnek | +420 532 290 361 | 107 | [javascript protected email address] |
Project number | Name | Investigator |
---|---|---|
25-15763S | doc. Ing. Jan Klusák, Ph.D. | |
25-15755S | Ing. Lucie Malíková, Ph.D. | |
4000144907/24/NL/AR | SteeLs improved by Oxides and Nitrides dispersion for launchers applications (SLON) | doc. Ing. Jan Klusák, Ph.D. |
8J24AT001 | Damage initiation of concrete with recycled aggregates - fracture properties and role of interface (DICRAgg) | Ing. Petr Miarka, Ph.D. |
CZ.02.01.01/00/22_008/0004631 | Materials and technologies for sustainable development (MATUR) | Ing. Petr Miarka, Ph.D. |
Project number | Name | Investigator |
---|---|---|
4000138900/22/NL/GP/gg | Characterisation of Thermal and Mechanical Performance of SIM Cryostat Straps (CRYSA) | doc. Ing. Jan Klusák, Ph.D. |
8J22AT008 | Mechanical fracture quantification of role of hemp fibres on self-healing processes in selected composites (KvaRK) | doc. Ing. Stanislav Seitl, Ph.D. |
21-14886S | Influence of material properties of high strength steels on durability of engineering structures and bridges | doc. Ing. Stanislav Seitl, Ph.D. |
CZ.01.1.02/0.0/0.0/20_321/0024649 | Ultrasonic devices for gigacycle fatigue testing of materials | doc. Ing. Jan Klusák, Ph.D. |
21-08772S | Influence of Self-Healing effects on structural fatigue life extension of structures made from high performance concrete (InShe) | doc. Ing. Stanislav Seitl, Ph.D. |
8J20AT013 | Integrity and durability aspects of recycled aggregates composites (InDuRAC) | doc. Ing. Jan Klusák, Ph.D. |
20-00761S | Influence of material properties of stainless steels on reliability of bridge structures | doc. Ing. Stanislav Seitl, Ph.D. |
8J18AT009 | Failure initiation and fracture of quasi-brittle building materials (FInFraM) | Ing. Lucie Malíková, Ph.D. |
CZ.01.1.02/0.0/0.0/15_019/0004505 | Complex design of girders from advanced concretes | doc. Ing. Stanislav Seitl, Ph.D. |
17-01589S | Advanced computational and probabilistic modelling of steel structures taking account fatigue damage | doc. Ing. Stanislav Seitl, Ph.D. |
16-18702S | AMIRI − Aggregate-Matrix-Interface Related Issues in silicate-based composites | doc. Ing. Jan Klusák, Ph.D. |
CZ.1.07/2.3.00/45.0040 | Science Academy - critical thinking and practical application of scientific and technical knowledge in real life | doc. Ing. Jan Klusák, Ph.D. |
7AMB1-4AT012 | Development of new testing configurations for determination of relevant values of fracture characteristics of cementitious composites (DeTeCon) | doc. Ing. Stanislav Seitl, Ph.D. |
M100411204 | Utilization of termographic techniques and advance probabilistic method for the efficient estimation of Wöhler curve parameters | doc. Ing. Stanislav Seitl, Ph.D. |
P105/11/0466 | Energetic and stress state aspects of quasi-brittle fracture – consequences for determination of fracture-mechanical parameters of silicate composites | doc. Ing. Stanislav Seitl, Ph.D. |
P104/11/0833 | Response of cement based composites to fatigue loading: advanced numerical modeling and testing | doc. Ing. Stanislav Seitl, Ph.D. |
P108/10/2049 | Crack initiation and propagation from interface-related singular stress concentrators | doc. Ing. Jan Klusák, Ph.D. |
M100410901 | Fracture mechanics description of three dimensional structures: numerical analysis and physical consequences of constraint | doc. Ing. Stanislav Seitl, Ph.D. |
KJB200410901 | Fracture of silicate based composites studied on core drilled specimens – numerical-modeling background for advanced fracture parameters determination | doc. Ing. Stanislav Seitl, Ph.D. |
101/08/1623 | Innovative techniques for assessment of residual life of bodies with fatigue | doc. Ing. Stanislav Seitl, Ph.D. |
101/08/0994 | Determination of conditions of failure initiation in bi-material wedges composed of two orthotropic materials | doc. Ing. Jan Klusák, Ph.D. |
103/08/0963 | Basic fatigue characteristic and fracture of advanced building materials | doc. Ing. Stanislav Seitl, Ph.D. |
101/04/P001 | The influence of constraint on threshold values of the stress intensity factor | doc. Ing. Stanislav Seitl, Ph.D. |
106/03/P054 | Linear Elastic Fracture Mechanics of Bi-material notches | doc. Ing. Jan Klusák, Ph.D. |
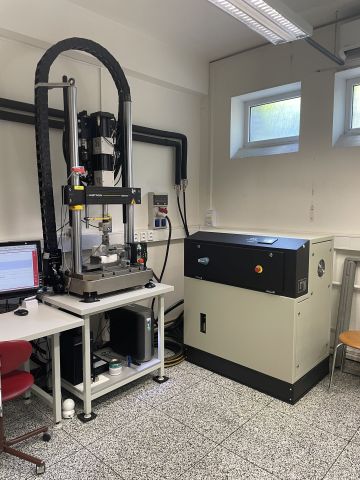
Contact person: Ing. Petr Miarka, Ph.D.
The servo-hydraulic pulsator is designed for static and dynamic testing of materials up to a force of 25 kN. The precision test control system allows control of the force and position (displacement) of the piston.
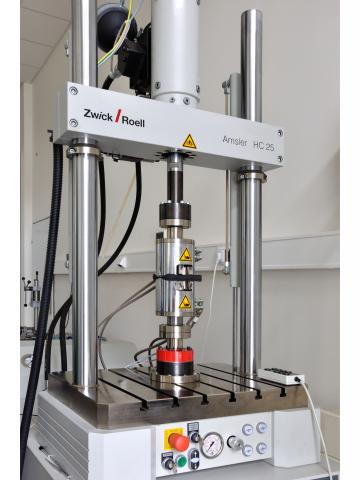
Contact person: Ing. Petr Miarka, Ph.D.
Compact table model of servo-hydraulic pulsator dedicated for static and dynamic material testing. Pulsator is capable to load the specimen by forces up to 25 kN. Maximum stroke of grips is 250 mm. Testing device is able to control mechanical tests in control regime of force or displacement. Electronic controlling system enables tailoring of a course of the mechanical test according to operator needs. Zwick/Roell Amsler HC25 is mainly determined for fatigue tests with low frequencies and with needs of fine level of control.
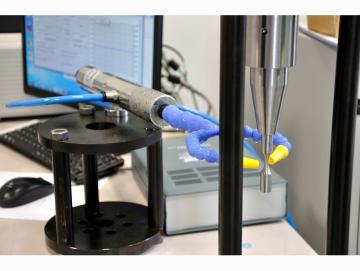
Contact person: doc. Ing. Jan Klusák, Ph.D.
Ultrasonic fatigue system pulsating at frequency of 20 kHz. This allows real-time measurement of very high cycle fatigue properties of materials at the number of cycles between 10 million to 10 billion. Measurement is possible under tension/compression and tension/tension conditions. It enables the measurement of SN (Wöhler) curves and fatigue crack propagation rates.
all publications