Electromechanical test system ZWICK Z250
Contact | Ing. Zdeněk Balík |
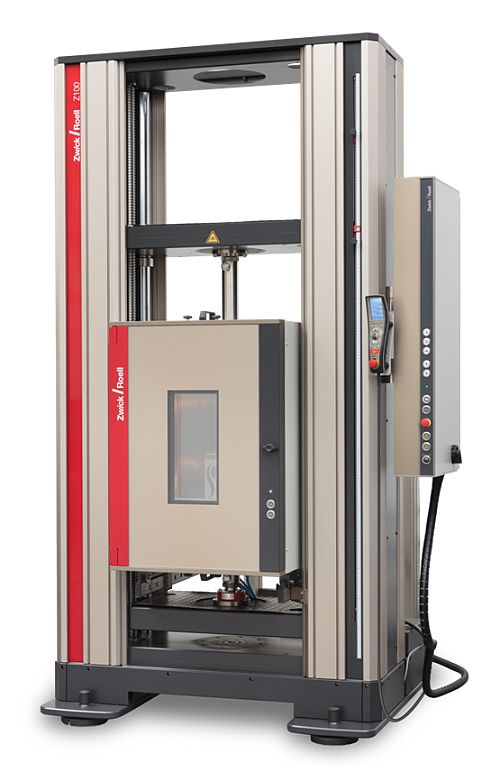
The universal test system enabling force loading up to 250 kN is mainly used for quasi-static testing of various loading modes like tensile, pressure, bend and fracture toughness testing for a wide range of materials especially for metals, polymers or possibly ceramics and theirs composites in a relatively wide temperature range.
The maximum force capacity of the system is up to ± 250 kN. The applicable force range of the mechanical tests depends also on the type and size of the fixtures. Following test assembly can be used: mechanical jaws (capacity 250 kN) allowing camping of round and flat tensile specimens, the jigs for 3 and 4 – point bend (capacity 100 kN) with a range of rollers from 40 to 400 mm and pressure plates (capacity 100 kN). For fracture mechanics testing of CT specimens, the clevises with a capacity 100 kN are available. There are also other specialised clamping jigs of our in-house production. The test system is equipped with an environmental chamber (internal dimensions (mm): height 850, width 450, depth 560) enabling testing in the temperature range -80 to +250 ° C. Low-temperature cooling is realized by vapours of liquid nitrogen. For further lower temperatures up to approx. -160 ° C, a cryostat of our design cooled by vapours of liquid nitrogen is available, suitable mainly for tensile and fracture toughness testing. The system is fully controlled by TestXpert II - V3.6 software with a high degree of variability and the ability to modify test procedures allowing complex experiments to be performed. Deformation of samples can be measured using contact or contactless systems. At room temperature, a MultiXsens contact deformation sensor (tension configuration, 3 and 4 – point bending) is available for deformation measurement. For other temperatures, specimen’s deformation can be measured by a wide range of contact sensors of brands like Sandner, MTS and EpsilonTech. Non-contact measurement of specimen’s deformations can be realized in 2D using DIC or in 3D using ESPI DantecDynamic Q300. Furthermore, it is possible to use additional methods to support mechanical experiments, such as monitoring crack propagation using acoustic emission with the system Dakel IPL, or crack length monitoring by a potential method using the system Techlab.